Unveiling the Innovations of Stryker Drill Bits: Precision and Durability Explored
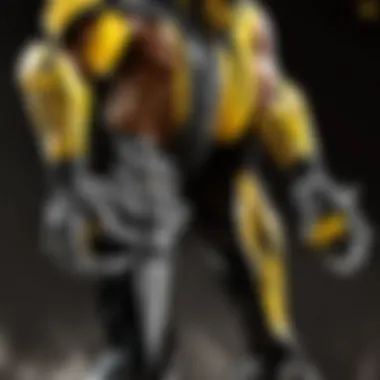
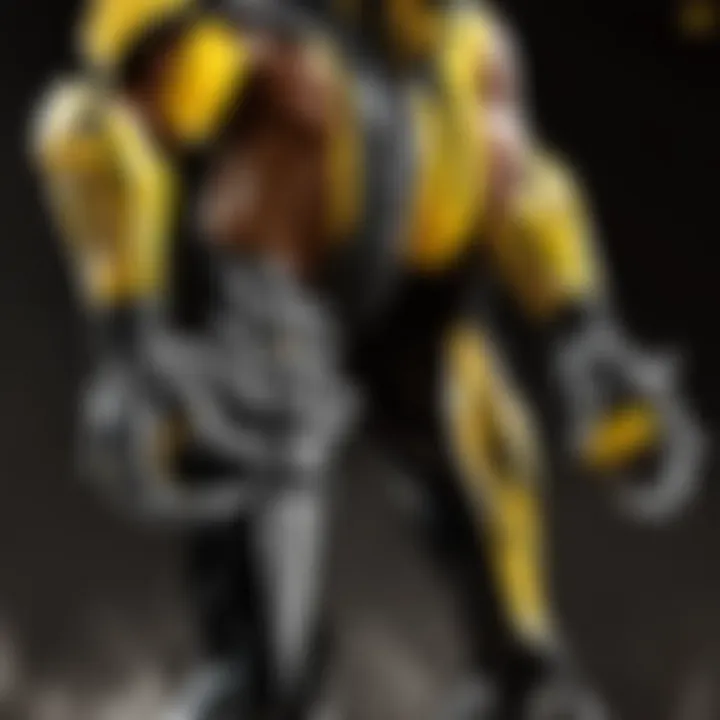
Character Profiles & Movesets
In delving into the fascinating realm of Stryker drill bits, we first encounter an ingenious creation born out of meticulous research and engineering excellence. These drill bits boast a unique design that sets them apart in the realm of cutting-edge drilling technology. Like skilled combatants in a fierce battle, Stryker drill bits showcase unparalleled precision and durability, making them indispensable tools in a variety of fields from orthopedic surgeries to industrial applications. As we uncover the intricacies of their design and operation, we come to appreciate the ingenuity that underpins their utility.
Gameplay Strategies & Tactics
When harnessing the power of Stryker drill bits, much like devising strategies for a complex video game, it is essential to understand the nuances of their functionality. Strategies for optimal utilization vary across different drilling scenarios, much like adapting gameplay tactics to diverse gaming modes and difficulty levels. By delving into the tactics for countering obstacles and maximizing drilling efficiency, we unlock the true potential of these formidable tools. Insights into the mechanics of drilling operations provide us with a strategic advantage, akin to mastering specific matchups in a challenging game setting.
Storyline & Lore Explorations
Amidst the mechanical precision of Stryker drill bits lies a narrative of innovation and evolution that mirrors the immersive storytelling found in compelling video game worlds. As we analyze the overarching plot of technological advancements and subplots of industrial applications, we uncover a rich tapestry of engineering lore. Delving into the intricate relationships between materials and performance unveils a narrative akin to character-driven stories, offering insights into the development of drill bit technologies. Speculating on future advancements and potential crossovers between different tool platforms adds an element of intrigue similar to unfolding storyline arcs.
Updates & Patch Notes
Just as game developers release updates and patches to enhance player experience, the world of Stryker drill bits evolves with new releases and technical improvements. Coverage of the latest updates and DLC releases in drill bit design sheds light on the continuous quest for innovation and performance optimization. Analyzing the impact of new features and gameplay changes post-update offers valuable insights into the evolving landscape of drilling technology. By comparing pre and post-patch mechanics, we gain a comprehensive understanding of the iterative nature of technological advancements in the realm of precision engineering and drilling applications.
Introduction to Stryker Drill Bits
In the realm of precision engineering and technological advancements, Stryker Drill Bits stand out as innovative tools that have redefined drilling practices across various industries. These drill bits possess advanced features and capabilities that optimize the process of creating boreholes with unparalleled accuracy and efficiency. The importance of understanding the intricacies of Stryker Drill Bits lies in their widespread applications, from orthopedic surgeries necessitating utmost precision to industrial settings demanding robust performance.
Evolution of Drill Bit Technology
Early Drill Bit Designs
Delving into the origins of drill bit technology unveils the evolution of early drill bit designs that laid the foundation for contemporary tools such as Stryker Drill Bits. These designs, though simplistic compared to modern iterations, incorporated groundbreaking concepts that set the stage for technological advancements. Early drill bit designs emphasized durability and effectiveness, with materials like hardened steel enabling efficient drilling in various materials. While these designs lacked the sophistication of current options, they were instrumental in shaping the trajectory of drill bit engineering.
Technological Advancements
The progression of drill bit technology has been marked by significant advancements that have enhanced precision and performance. Technological innovations, such as the integration of cutting-edge materials and manufacturing techniques, have revolutionized the capabilities of drill bits. Stryker Drill Bits, with their incorporation of state-of-the-art technologies, exemplify the culmination of years of research and development in the field. These advancements have propelled drill bits to new heights of efficiency and reliability, catering to diverse industry requirements with precision and finesse.
Role of Stryker Drill Bits
Precision Engineering
At the core of Stryker Drill Bits lies precision engineering, a fundamental aspect that elevates their functionality to unparalleled levels. The meticulous design and calibration of these drill bits ensure consistent and accurate drilling outcomes, crucial for intricate procedures in various domains. Precision engineering in Stryker Drill Bits translates to minimized errors and enhanced operational efficiency, reflecting a commitment to excellence in tool development.
Diverse Applications
Stryker Drill Bits' versatility shines through their diverse applications across multiple sectors, from healthcare to manufacturing. The adaptability of these drill bits to varying operational demands underscores their value as reliable and adaptable tools. Whether in orthopedic surgeries requiring intricate bone drilling or industrial settings demanding precise machining, Stryker Drill Bits offer tailored solutions that cater to a range of user needs.
Significance in Orthopedic Surgeries
Enhanced Precision in Medical Procedures
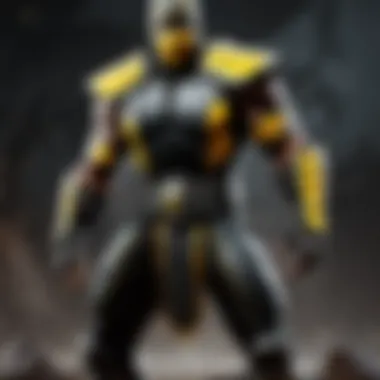
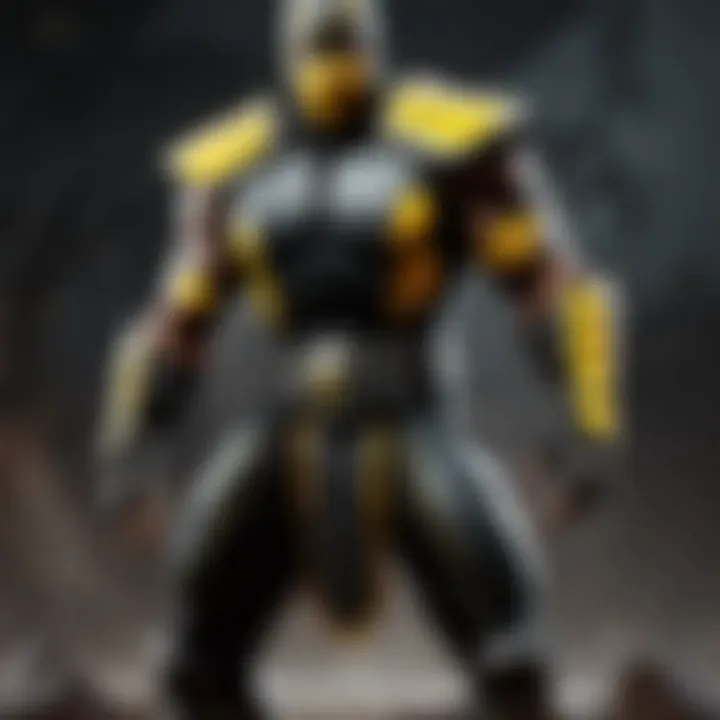
The application of Stryker Drill Bits in orthopedic surgeries plays a pivotal role in achieving enhanced precision during medical procedures. The specialized design of these drill bits enables surgeons to navigate delicate anatomical structures with accuracy and confidence, ensuring optimal surgical outcomes. With a focus on instrument precision, Stryker Drill Bits contribute significantly to the success and safety of orthopedic interventions, heralding a new era of surgical efficacy.
Benefits for Surgeons and Patients
The advantages of using Stryker Drill Bits extend beyond surgical precision to encompass tangible benefits for both surgeons and patients. Surgeons experience improved procedural efficiency and control, thanks to the reliable performance of these drill bits. Concurrently, patients benefit from reduced operative times and minimized tissue trauma, translating to enhanced post-operative recovery and overall satisfaction. The symbiotic relationship between Stryker Drill Bits and the orthopedic surgical context underscores their transformative impact on patient care and surgical success.
Key Features of Stryker Drill Bits
In the realm of drilling technology, the key features of Stryker drill bits stand out as indispensable components crucial for precision and efficacy. These features encompass a blend of cutting-edge design elements and advanced functionalities tailored to meet the demands of various industries. Understanding the significance of these features is paramount in grasping the transformative nature of Stryker drill bits in reshaping drilling practices.
Advanced Design Elements
Material Composition
The material composition of Stryker drill bits plays a pivotal role in their overall performance and durability. Comprising high-quality alloys and metals, the material composition ensures robustness and resistance to the demanding conditions they encounter during operations. This specialized material blend not only enhances the longevity of the drill bits but also contributes to their precision and effectiveness in drilling applications. While the material composition may vary based on the specific requirements of different industries, the common thread lies in the reliability and resilience that this choice offers for optimal drilling outcomes.
Cutting Edge Technology
Embracing cutting-edge technology, Stryker drill bits integrate innovative cutting mechanisms that elevate drilling standards to new heights. The precision engineering behind the cutting edge technology enables swift and accurate drilling, minimizing errors and maximizing efficiency. One distinctive feature of this technology is its ability to adapt to diverse drilling tasks, ensuring versatility and adaptability across various industrial settings. Despite its complexities, the cutting-edge technology implemented in Stryker drill bits remains user-friendly, facilitating seamless operations and enhancing productivity.
Customization Options
Tailored Solutions for Different Industries
The provision of tailored solutions for different industries underscores Stryker drill bits' commitment to meeting industry-specific needs effectively. By customizing drill bits to align with the unique requirements of diverse sectors such as orthopedic surgery, manufacturing, and construction, Stryker ensures optimum performance and output. These tailored solutions not only enhance operational efficiency but also address the nuanced challenges faced by professionals in each sector, thus streamlining their drilling processes for heightened productivity.
Specialized Configurations
Stryker drill bits offer specialized configurations that cater to the intricacies of varied drilling tasks, further emphasizing their adaptability and precision. These configurations are meticulously designed to optimize performance in specific applications, facilitating smoother drilling operations and bolstering overall efficiency. By incorporating specialized configurations into their product range, Stryker enables professionals to tackle complex drilling requirements with ease, ensuring exceptional outcomes and customer satisfaction.
Durability and Longevity
High-Quality Materials
At the core of Stryker drill bits' durability and longevity lie high-quality materials crafted to withstand rigorous usage and challenging environments. These materials, meticulously selected for their strength and resilience, ensure that the drill bits deliver consistent performance over extended periods. The emphasis on high-quality materials not only enhances the operational lifespan of the drill bits but also reduces maintenance requirements, optimizing cost-effectiveness for users across various industries.
Resistance to Wear and Tear
Stryker drill bits boast impressive resistance to wear and tear, owing to their robust construction and specialized manufacturing processes. This resistance not only prolongs the lifespan of the drill bits but also maintains their sharpness and precision throughout numerous drilling operations. By minimizing wear and tear, Stryker drill bits guarantee sustained performance levels, minimizing downtime and maximizing operational efficiency for users in demanding industrial environments.
Applications of Stryker Drill Bits
In this detailed exploration of Stryker Drill Bits, their applications play a pivotal role in showcasing the versatility and precision of these cutting-edge tools. From orthopedic surgery to various industrial sectors, Stryker Drill Bits have become indispensable in the realm of drilling technology. These bits are carefully engineered to ensure optimal performance across a range of applications, offering tailored solutions for specific industries and procedures. The impact of Stryker Drill Bits goes beyond mere functionality, as they revolutionize how drilling tasks are approached, emphasizing efficiency, accuracy, and durability.

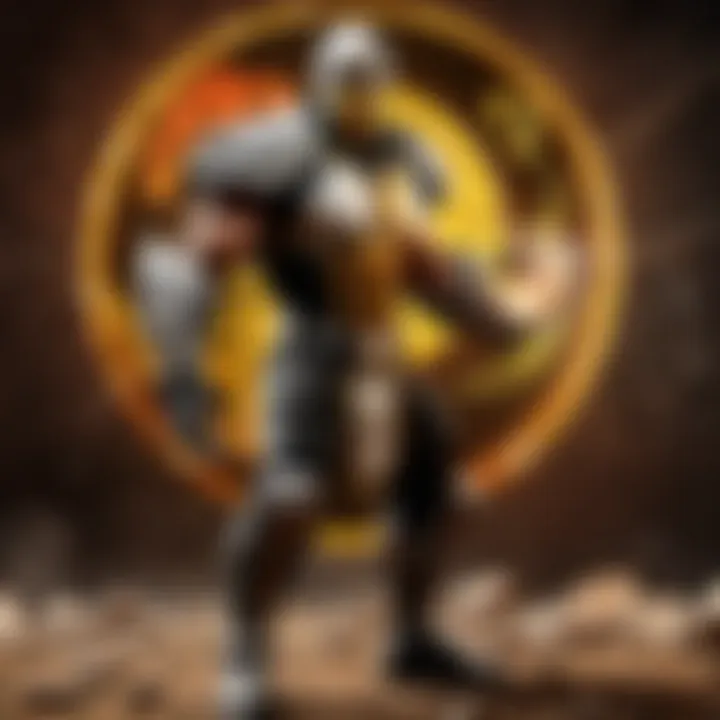
Orthopedic Surgery
Bone Drilling Procedures
Within the field of orthopedic surgery, Bone Drilling Procedures stand out as a crucial application of Stryker Drill Bits. These procedures involve the precise drilling of bones during surgeries, requiring tools that can guarantee accurate and consistent results. Stryker Drill Bits excel in Bone Drilling Procedures due to their advanced design elements, such as high-quality material composition and cutting-edge technology. The unique feature of these bits lies in their ability to minimize errors and ensure minimal disruption to surrounding bone structure, enhancing the overall surgical outcome. Surgeons rely on the reliability and precision of Stryker Drill Bits for bone drilling, appreciating the efficiency and effectiveness these tools bring to orthopedic interventions.
Joint Replacements
Another key aspect of orthopedic surgery where Stryker Drill Bits shine is in the domain of Joint Replacements. During joint replacement surgeries, precision is paramount to ensure the proper fitting of prosthetic components. Stryker Drill Bits offer unique features tailored for such procedures, facilitating accurate and controlled drilling to accommodate implant placement. The high-quality materials and specialized configurations of these bits contribute to their success in joint replacement surgeries, allowing surgeons to achieve optimal results with reduced risk of complications. The advantages of using Stryker Drill Bits in joint replacements include enhanced surgical precision, reduced operating time, and improved patient outcomes.
Industrial Manufacturing
Metal Fabrication
In the industrial manufacturing sector, the application of Stryker Drill Bits in Metal Fabrication processes underscores their reliability and efficiency. Metal fabrication entails the shaping and assembling of metal structures through drilling, cutting, and shaping techniques. Stryker Drill Bits offer a key advantage in metal fabrication due to their durability and resistance to wear and tear, ensuring consistent performance in challenging industrial environments. The unique feature of these bits lies in their ability to maintain sharpness and stability during prolonged use, optimizing the fabrication process and promoting efficiency. Manufacturers leverage the precision and longevity of Stryker Drill Bits in metal fabrication to enhance productivity and product quality.
Precision Machining
Precision machining operations rely on Stryker Drill Bits for their unmatched accuracy and performance in intricate machining tasks. These bits are customized to meet the demands of precision machining, guaranteeing the meticulous removal of material to achieve desired dimensions and surface finishes. The key characteristic of Stryker Drill Bits in precision machining is their ability to deliver fast drilling speeds without compromising accuracy, resulting in expedited production cycles and superior components. Manufacturers value the versatility and consistency of these bits in precision machining applications, enabling them to meet tight tolerances and exacting specifications with ease.
Construction Sector
Concrete Drilling
Within the construction sector, Stryker Drill Bits find extensive use in Concrete Drilling operations, demonstrating their robustness and reliability in challenging construction projects. Concrete drilling involves the penetration of concrete surfaces for various purposes, such as installation of fixtures, anchor bolts, or structural modifications. Stryker Drill Bits excel in concrete drilling due to their specialized configurations and resistance to abrasive materials, allowing for efficient and precise drilling without compromising bit integrity. The unique feature of these bits lies in their ability to maintain sharpness and stability even when subjected to hard concrete surfaces, ensuring consistent performance throughout the drilling process. Construction professionals rely on the durability and effectiveness of Stryker Drill Bits in concrete drilling tasks, streamlining project timelines and minimizing downtime.
Infrastructure Development
In infrastructure development projects, Stryker Drill Bits play a vital role in expediting drilling tasks for the creation of essential structures and facilities. Infrastructure development encompasses various construction activities aimed at enhancing public amenities, transportation networks, and urban landscapes. Stryker Drill Bits offer a key advantage in infrastructure development by providing efficient and accurate drilling solutions for diverse project requirements. The unique feature of these bits lies in their adaptability to different drilling conditions, ensuring optimal performance across various construction materials and environments. Engineers and contractors rely on the precision and longevity of Stryker Drill Bits in infrastructure development projects to meet deadlines, maintain quality standards, and optimize resource utilization.
Benefits of Using Stryker Drill Bits
When it comes to the realm of drilling technology, the benefits of utilizing Stryker drill bits cannot be overstated. These cutting-edge tools offer precision, durability, and efficiency, making them indispensable in various industries. One key element that sets Stryker drill bits apart is their ability to minimize errors during drilling procedures. This feature ensures that surgeries, manufacturing processes, or construction tasks are carried out with the utmost accuracy, reducing the risk of any mistakes. The minimized errors attribute of Stryker drill bits is a game-changer, guaranteeing consistent and reliable performance in every operation.
Moving on to the aspect of consistent performance, Stryker drill bits excel in delivering unwavering results across the board. Their design and technology facilitate a seamless drilling experience, where operators can rely on the tools to perform consistently with each use. This consistency not only boosts productivity but also instills confidence in the accuracy of the drilling process. Stryker drill bits' consistent performance is a hallmark of their quality, making them a top choice for professionals across different sectors.
Precision and Accuracy
Minimized Errors
Discussing the concept of minimized errors in more detail unveils the meticulous engineering put into Stryker drill bits. These tools are engineered to mitigate any deviations during drilling, ensuring precise outcomes in orthopedic surgeries, industrial applications, and construction projects. The unique feature of minimized errors lies in its ability to enhance surgical precision, improve product quality in manufacturing, and streamline drilling in construction, offering unmatched advantages across diverse fields.
Consistent Performance

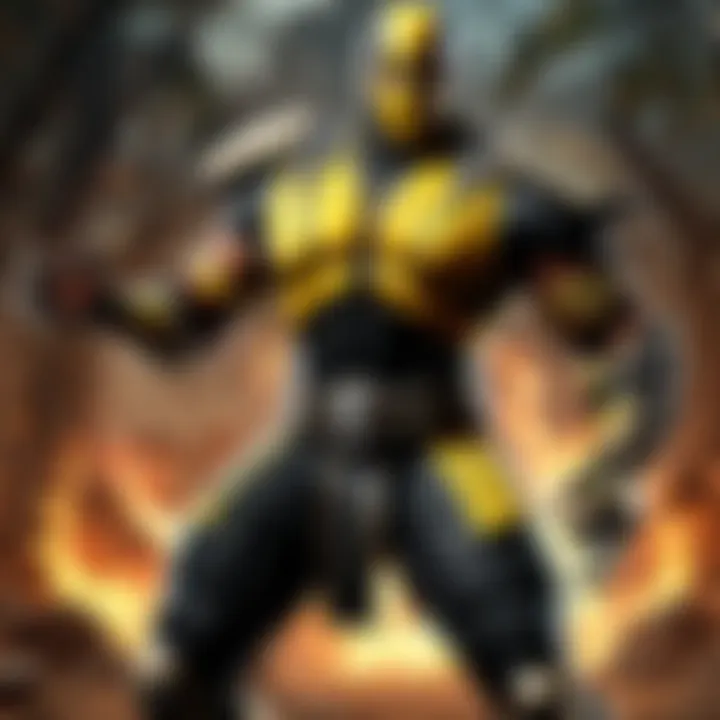
The consistent performance of Stryker drill bits reflects a commitment to excellence in drilling technology. By providing reliability in every operation, these tools enable professionals to achieve consistent results without fluctuations in performance. This reliability is a significant advantage, especially in critical procedures where precision and repetition are paramount. Stryker drill bits stand out for their consistent performance, serving as a benchmark for quality and efficiency.
Efficiency in Operations
Faster Drilling Speeds
In the realm of drilling, time is of the essence, and Stryker drill bits excel in offering faster drilling speeds. This attribute accelerates the drilling process, reducing overall operation duration and enhancing efficiency. The key characteristic of faster drilling speeds lies in the optimization of cutting mechanisms and material compositions, resulting in swift and precise drilling actions. The unique feature of faster drilling speeds contributes to productivity gains, making Stryker drill bits a preferred choice for high-volume drilling requirements.
Reduced Downtime
Another crucial aspect of operational efficiency is reduced downtime, a benefit that Stryker drill bits deliver effectively. By minimizing interruptions during drilling tasks, these tools ensure continuous workflow and optimal utilization of time and resources. The key characteristic of reduced downtime is its ability to streamline operations, minimize delays, and maximize productivity. The unique feature of reduced downtime offers a competitive edge, allowing for seamless operations and faster project completion.
Cost-Effectiveness
Long Service Life
The long service life of Stryker drill bits is a testament to their durability and high-quality construction. These tools are designed to withstand rigorous usage, ensuring prolonged functionality and performance consistency over extended periods. The key characteristic of long service life lies in the superior materials and craftsmanship employed in their production, guaranteeing longevity and reliability. The unique feature of long service life results in cost savings, as fewer replacements are needed, making Stryker drill bits a cost-effective investment.
Savings on Replacement Costs
One of the significant advantages of choosing Stryker drill bits is the potential savings on replacement costs. Due to their durability and resilience, these tools reduce the frequency of replacements, cutting down on operational expenses in the long run. The key characteristic of savings on replacement costs is the financial benefits accrued from extended tool lifespan and reduced maintenance requirements. The unique feature of savings on replacement costs reinforces the cost-effectiveness of using Stryker drill bits, making them a strategic choice for businesses looking to optimize their drilling operations.
Future Trends in Drill Bit Technology
In the realm of drill bit technology, staying updated on future trends is of paramount importance. The evolution of materials and designs directly impacts the efficiency and effectiveness of drilling operations. By focusing on future trends, industries can significantly improve their production processes and outcomes. The ongoing advancements in drill bit technology pave the way for enhanced performance and durability in various applications. Whether in orthopedic surgeries or industrial manufacturing, being abreast of the latest trends ensures staying competitive and pushing boundaries.
Innovations in Materials
Nano-coatings:
Nano-coatings play a pivotal role in enhancing the durability and precision of drill bits. These ultra-thin layers of coating provide increased resistance to wear and corrosion, prolonging the lifespan of the drill bit. Nano-coatings offer a smoother surface finish, reducing friction during drilling and enabling higher drilling speeds. The nano-scale thickness of these coatings allows for intricate detailing on the drill bits, improving their overall performance and longevity.
Composite Materials:
Composite materials revolutionize the industry with their high strength-to-weight ratio and corrosion resistance. Incorporating various elements like carbon fiber and polymer matrices, composite materials enhance the durability and flexibility of drill bits. Their ability to withstand extreme conditions and impact forces make them a preferred choice in demanding drilling environments. The unique feature of composite materials lies in their adaptability to different applications, providing tailored solutions for various industries.
Smart Drill Bit Technology
In a world driven by data and analytics, integrating smart technologies into drill bits has become essential. Sensor integration enables real-time monitoring of drilling conditions, such as temperature and pressure, optimizing drilling parameters for improved efficiency and performance. By collecting and analyzing data through embedded sensors, drill bits can adjust their operations dynamically, reducing errors and downtime. The incorporation of data analytics enhances decision-making processes, offering valuable insights for process optimization and predictive maintenance.
Environmental Sustainability
Recyclable Materials:
The shift towards recyclable materials in drill bit manufacturing reflects a growing emphasis on sustainability and eco-friendliness. Choosing recyclable materials minimizes environmental impact by reducing waste generation and energy consumption during production. These materials can be repurposed or recycled after use, contributing to a circular economy and reducing the carbon footprint of drilling activities. The unique feature of recyclable materials lies in their closed-loop nature, promoting responsible resource management and ecological preservation.
Energy-Efficient Designs:
Energy-efficient designs focus on minimizing energy consumption and optimizing performance in drill bit operations. By reducing power requirements and improving operational efficiency, energy-efficient designs help lower operating costs and environmental impact. These designs leverage innovative mechanisms and materials to enhance drilling processes while conserving resources. The advantages of energy-efficient designs include lower carbon emissions, cost savings, and extended equipment lifespan, aligning with sustainability goals in drilling applications.